NuPlon™ Introduction
NuPlon is a novel formulation of plastic which can be used to provide an environmentally friendly solution to plastics pollution. The thermoset resin can be molded and machined to create pieces which biodegrade with water exposure over the course of 2-5 months.
NuPlon™ Resin
NuPlon resin is a proprietary curable pre-polymer comprised of hydroxyl and acid units which, upon heating, react with one another forming a chemically crosslinked solid by releasing a water molecule. The reaction is reversible as adding water back to the reaction mixture breaks the bonds and chemically degrades the structure down into small, non-toxic components. Typical degradation time is 2-3 months of exposure to water under moderately warm temperatures (86 °F, or 30 °C).
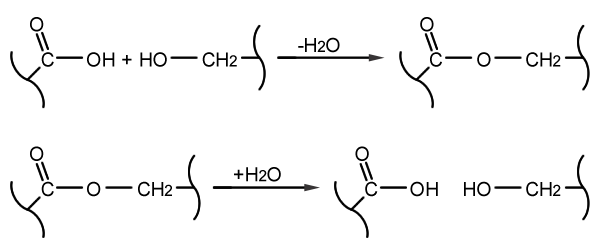
>Schematic chemical reaction of formation and degradation of NuPlon.
Pre-polymer Properties
The prepolymer is a viscous, clear, off-white liquid which can be poured out and handled as a liquid. It is medium viscosity at room temperature (~ 1500 – 2500 cP, Brookfield model LVDVE viscometer, #31 spindle, 5 RPM 20 °C)
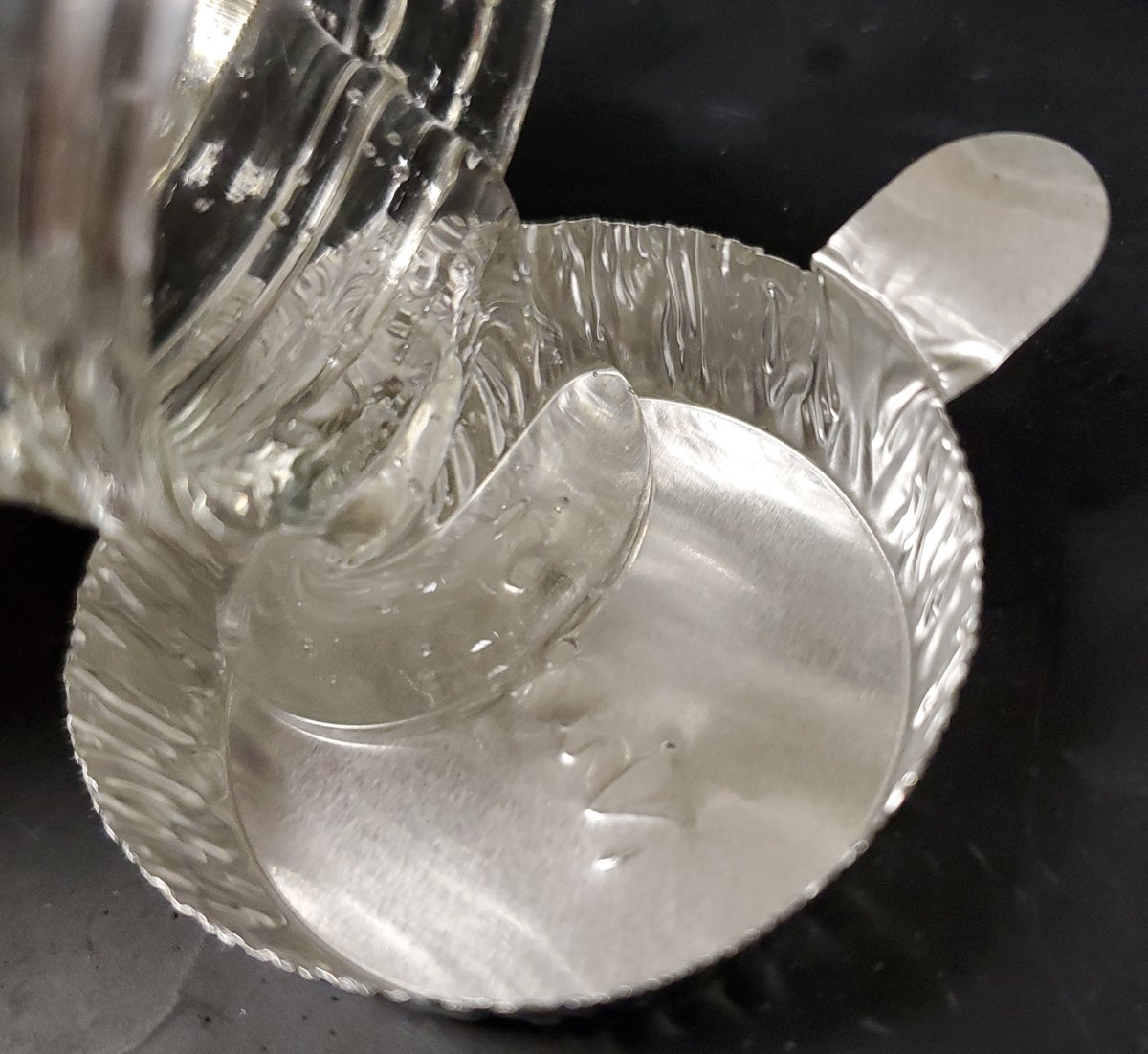
NuPlon prepolymer resin liquid.
The liquid can be poured into an open-top mold. As the liquid is adhesive and can form tight bonds, Akina has had the best success with flexible silicone molds coated with PTFE mold release spray (VDX, Microcare or equivalent). Additionally, thin, disposable metal molds may also be used. It is important for the molding assembly to have access to air to allow evaporation of water during curing.
Safety
Prior to curing, the prepolymer is an oligomeric mixture of short polyesters along with carboxylic acids and multi-functional alcohols. One of the major components is lactic acid, which contributes to the slightly ‘vinegar-like’ smell of the prepolymer. As lactic acid is moderately caustic, it is advised to avoid contact with skin or eyes, as well, it should not be ingested.
For curing processes, the substance must be heated. Follow all safety instructions provided by the manufacturer of the heating equipment you use for this process. As it cures, NuPlon will off-gas a small amount of lactic acid, which may be irritating to the eyes and nose. For this reason, curing should be performed only in well ventilated areas.
Curing
The process of curing NuPlon requires removal of water. This can be accomplished in an oven set to 130 ⁰C (266 ⁰F) or shorter times at higher temperatures up to ~ 170 °C (338 °F) above which darkening can occur. the typical curing time applied at Akina has typically been overnight (~10 – 24 hrs) for temperatures ~150 - 170 °C or over 2-3 days for temperatures ~120 – 150 °C. An indication of successful crosslinking is the formation of a solid which remains solid even at the curing temperatures (i.e. is not a liquid at 130 °C). As part of the curing process, it is important for the material to have good access to air-flow to evaporate away water. Note that whatever mold this curing occurs in will be the final shape of the material and it is suggested for the mold to be level to the ground to prevent pooling/puddling of the liquid.
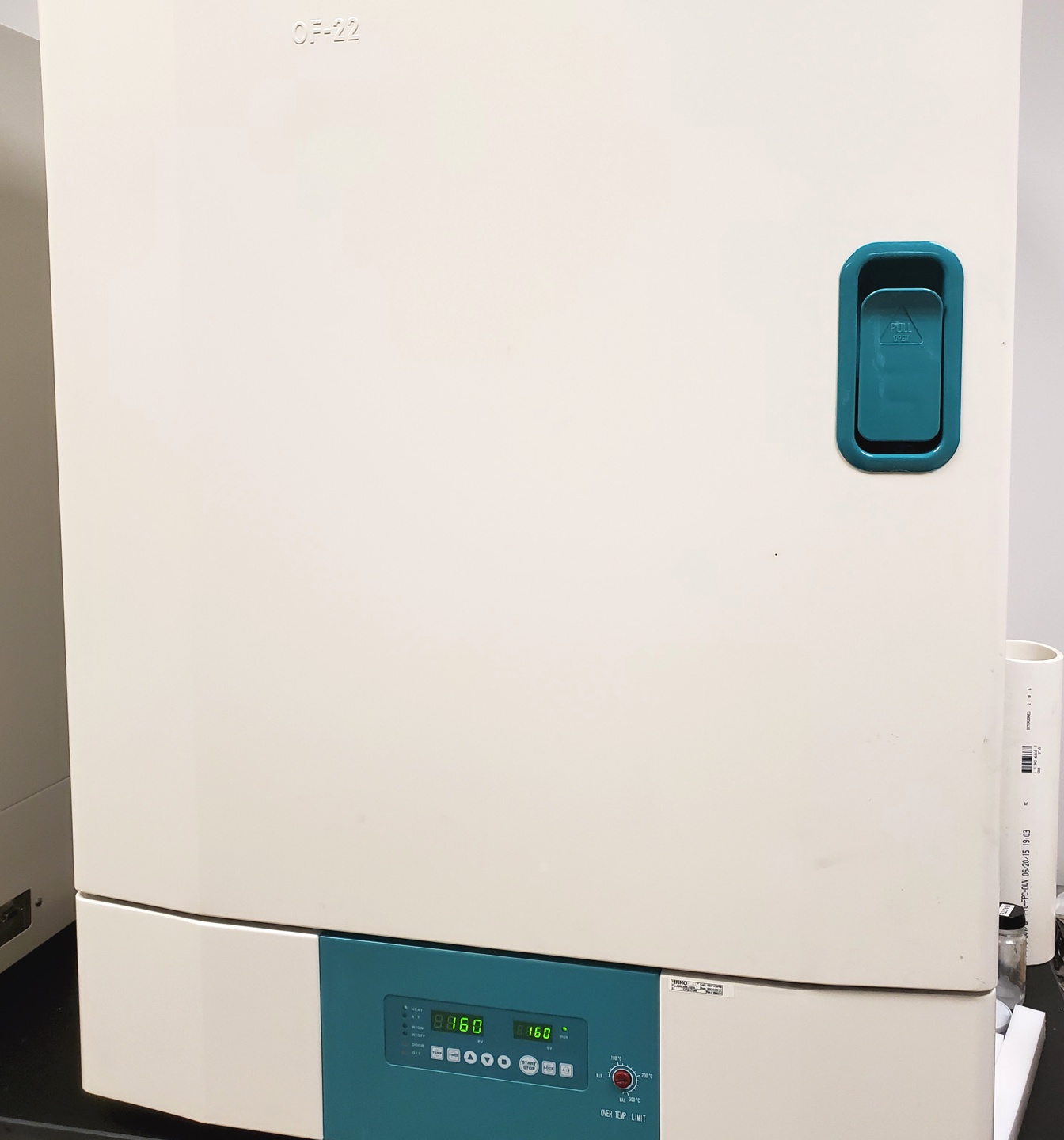
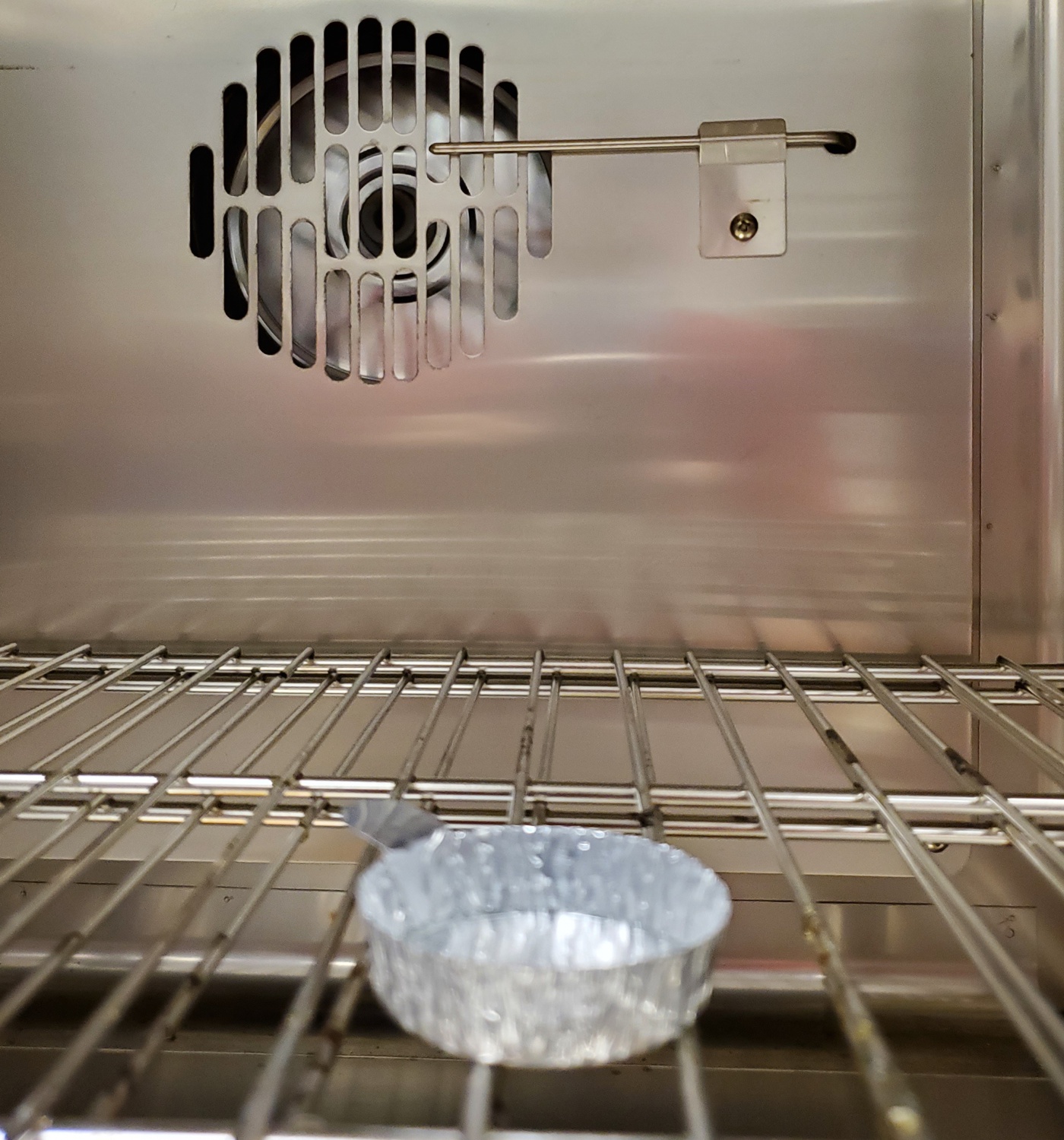
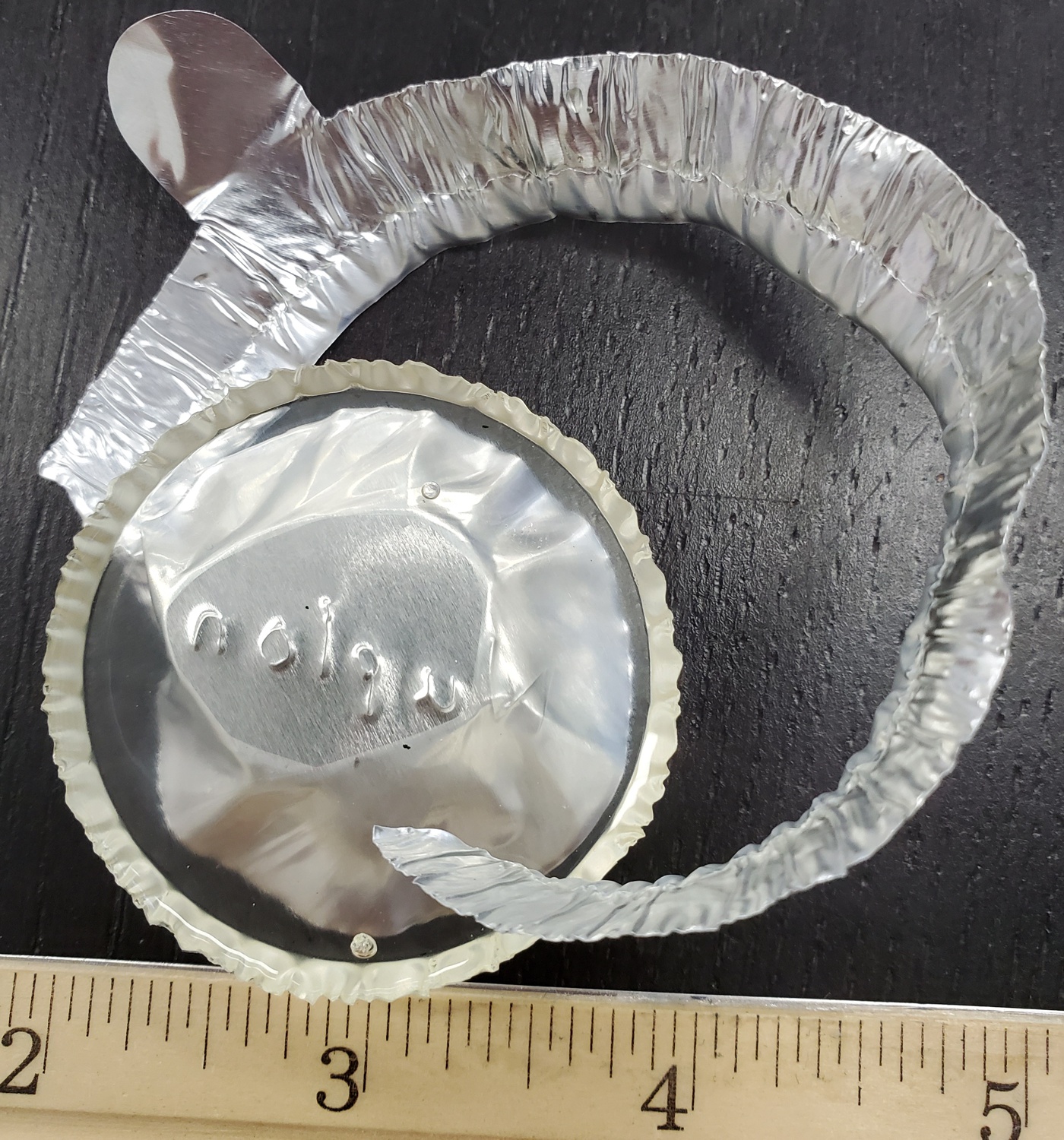
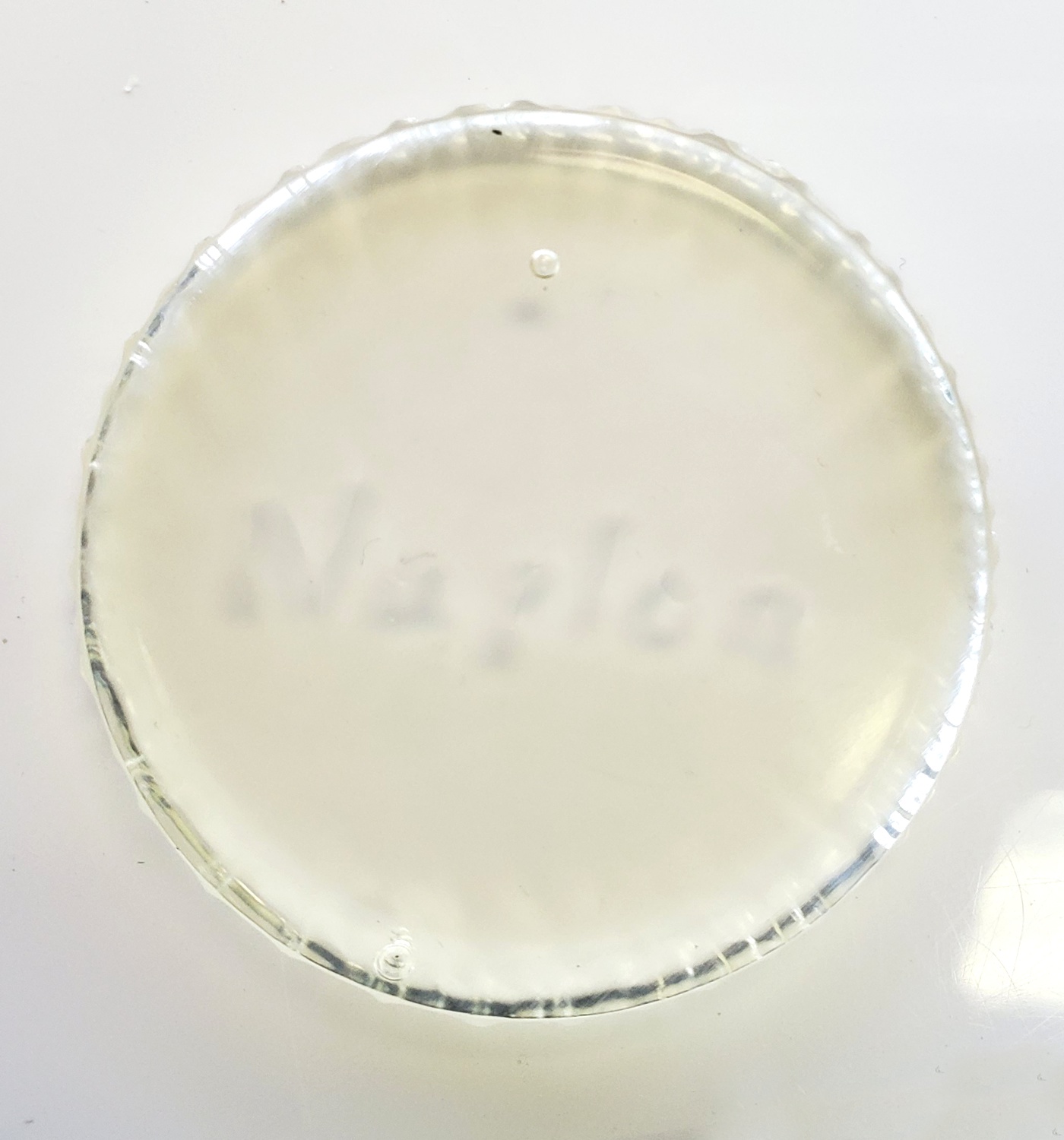
Curing process of forming NuPlon circle with “NuPlon” etched in the bottom of the mold.
The NuPlon can be optionally treated under vacuum to degas and vacuum can be used to assist in water removal. Despite this, the temperature must still be high enough for the chemical condensation reaction to occur and the vacuum does not change this. As an example, treating the NuPlon precursor under vacuum (-31 inHg) at 90 ⁰C overnight yielded a strongly adhesive viscoelastic material which was only partially crosslinked. As a side note, the application of purposefully performing partial-crosslinking the polymer to generate biodegradable adhesives remains a viable option for applications that need an adhesive. After the material is removed from the oven it can be cooled and de-molded.
Properties
Optical
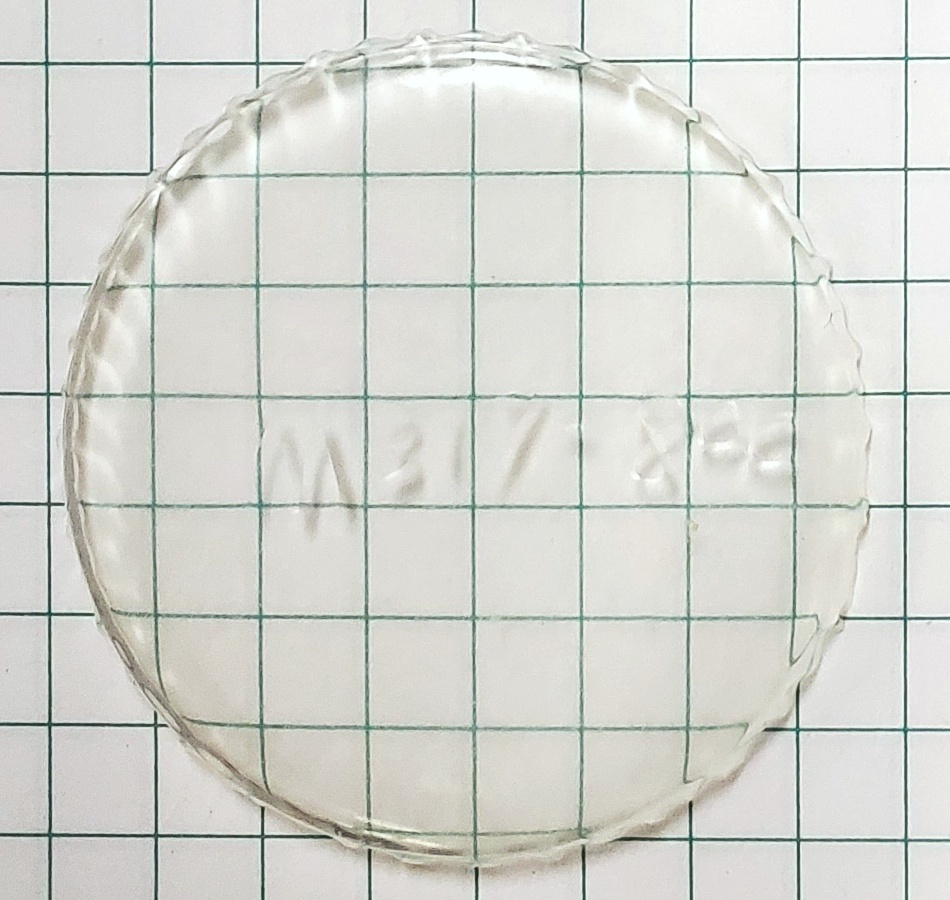
NuPlon piece resting on top of grid-paper.
NuPlon presents good spectral transparency within the visible light region. The data below is for type M317 NuPlon based on % transmittance through a 2 mm thick section of plastic.
Transmittance (%) of light at indicated wavelength.
NuPlon Type | % Transmittance at wavelength (nm) | Thickness (mm) | |||||||
---|---|---|---|---|---|---|---|---|---|
200 | 300 | 400 | 500 | 600 | 700 | 800 | 900 | ||
M317 | 0.1 | 0.8 | 72.9 | 87.1 | 88.6 | 88.9 | 89.0 | 87.8 | 2.0 |
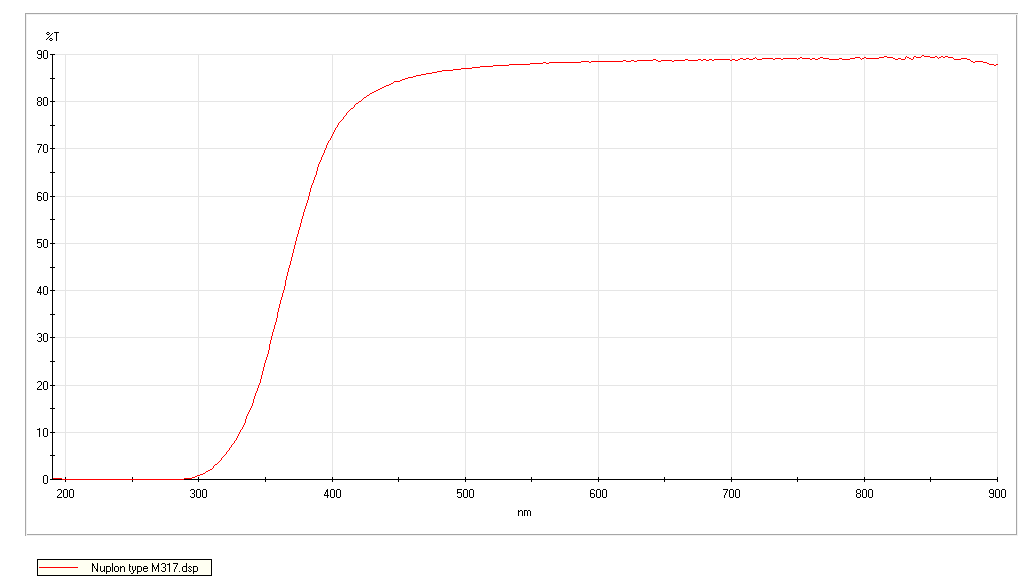
NuPlon UV-Vis Transmittance graph (type M317).
Given that transmittance drops to near-zero below 300 nm, NuPlon can be used to apply for ultra-violet shielding and protection.
Mechanical
Cured NuPlon type M317 in dry state is a hard, firm substance with the following mechanical properties
Mechanical properties of cured NuPlon (dog-bone test pieces, Tensile tested on TA.XTplus (Texture Technologies) at a crosshead speed of 1 mm/sec.) presented as average ± standard deviation, N = 2.
Property | Value |
---|---|
Elastic Modulus (0.1 – 1% strain) | 4.8 ± 1.6 MPa |
Tensile Strength | 31.0 ± 19.2 MPa |
Extensibility | 5.3 ± 1.6 % strain |
Thermal
NuPlon has unique properties in regard to its thermal behavior. Unlike thermoplastic materials, NuPlon does not melt nor does it become especially brittle with cold. Based on testing at Akina, NuPlon has been determined to be mechanically stable at temperatures between - 78 °C to 350 °C. This broad range of temperature stability applies only to the piece as it is dry due to its ability to be permeated by and affected by water.

Touching hot soldering iron to piece of cured NuPlon (type M317).
The thermal conductivity of NuPlon is relatively poor which enables it to be used as an insulator. It’s insulative properties can be enhanced by incorporation of sodium chloride (salt) at roughly 10 – 30% w/w of precursor before curing. Curing with sodium chloride creates a highly porous matrix which traps air and improves NuPlon’s thermal resistance.
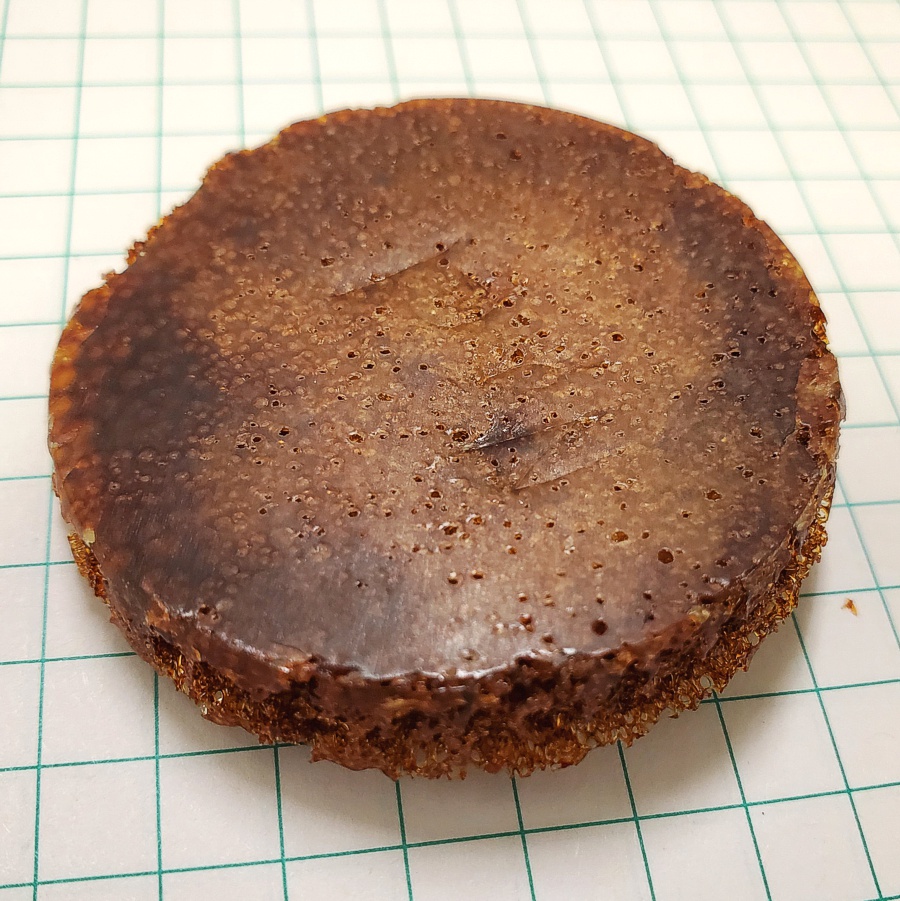
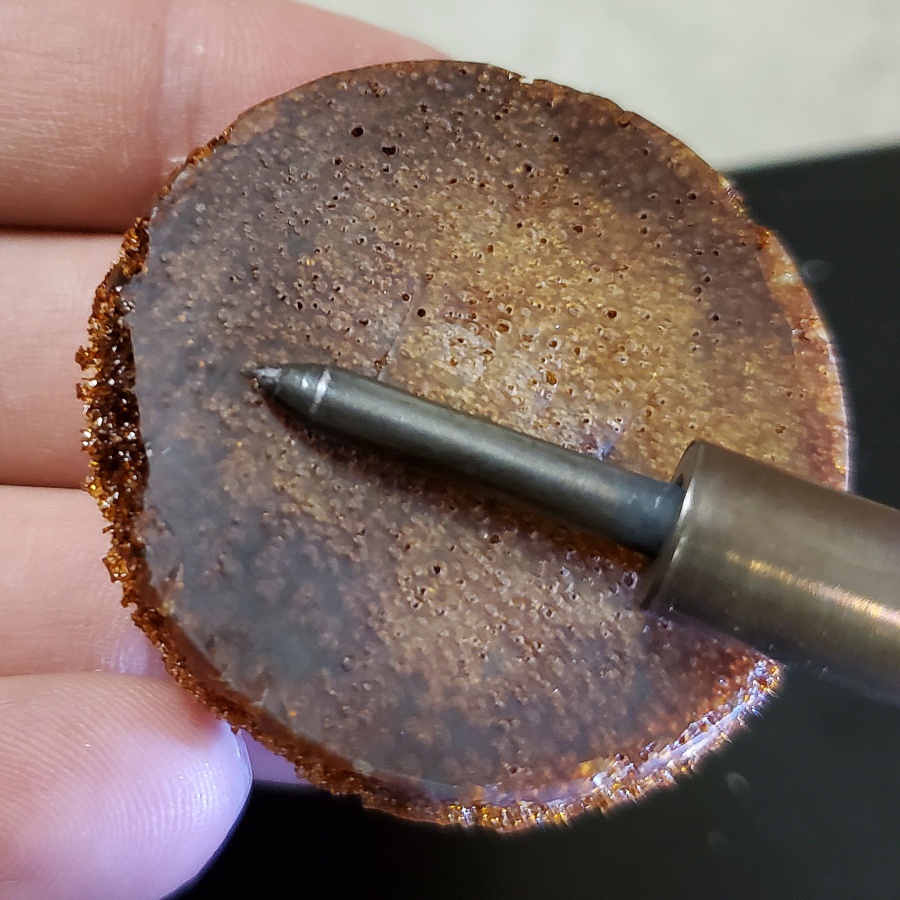
Salt-cured NuPlon, holding piece against soldering iron.
Degradability/Disposal
Within 1 day of exposure to water, NuPlon will become a highly plasticized, flexible material. It will remain whole, but flexible for up to 2-3 months (depending on temperature/water condition) after which point it will start to split up and break down eventually hydrolyzing to non-toxic water-soluble compounds. Testing at Akina, Inc. has indicated that type M317 NuPlon loses 93 ± 1% (Average ± STDEV, N = 3) of its mass after 2 months incubation at 30 °C with orbital agitation at 100 RPM in locally collected pond water.
Additionally, NuPlon, although not especially flammable, can be burned without formation of toxic fumes outside of typical carbon dioxide and other smoke components. Exposure to boiling hot water quickly forms a multitude of cracks within the NuPlon making it easy to break apart into smaller portions which degrade more quickly and are amenable to disposal.
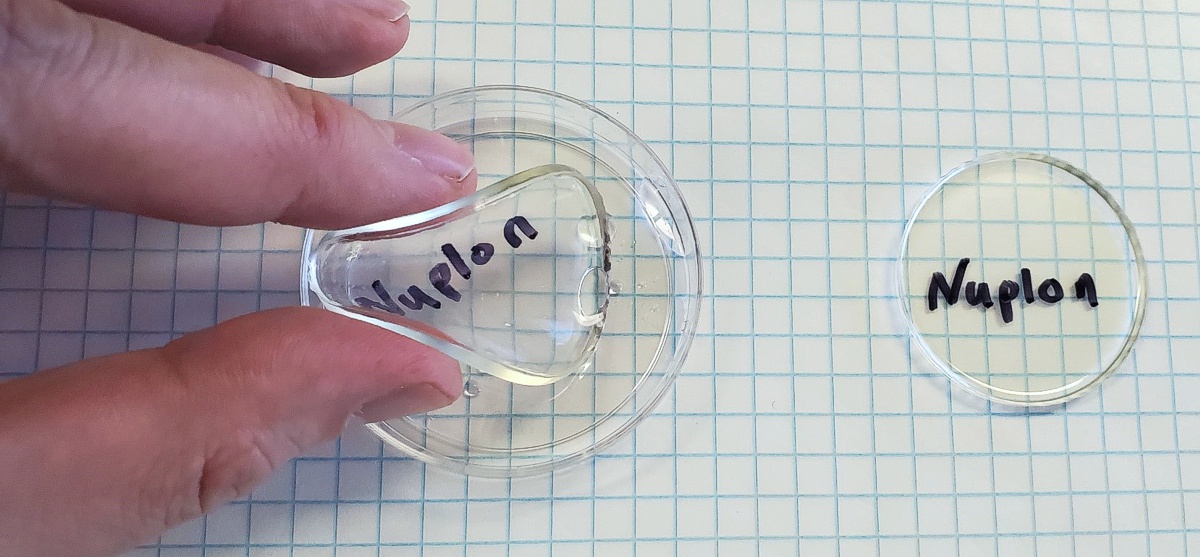
Examples of wet and dry NuPlon, respectively.
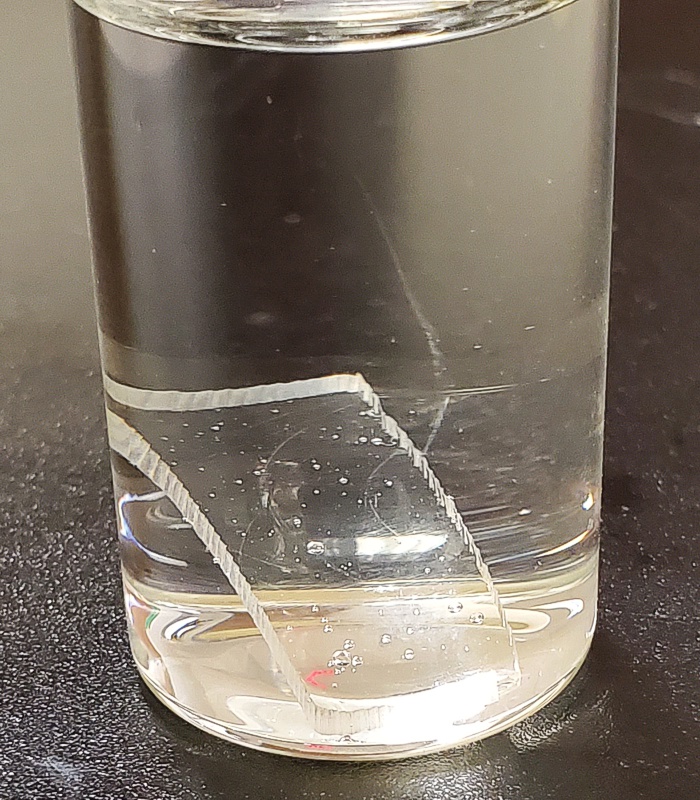
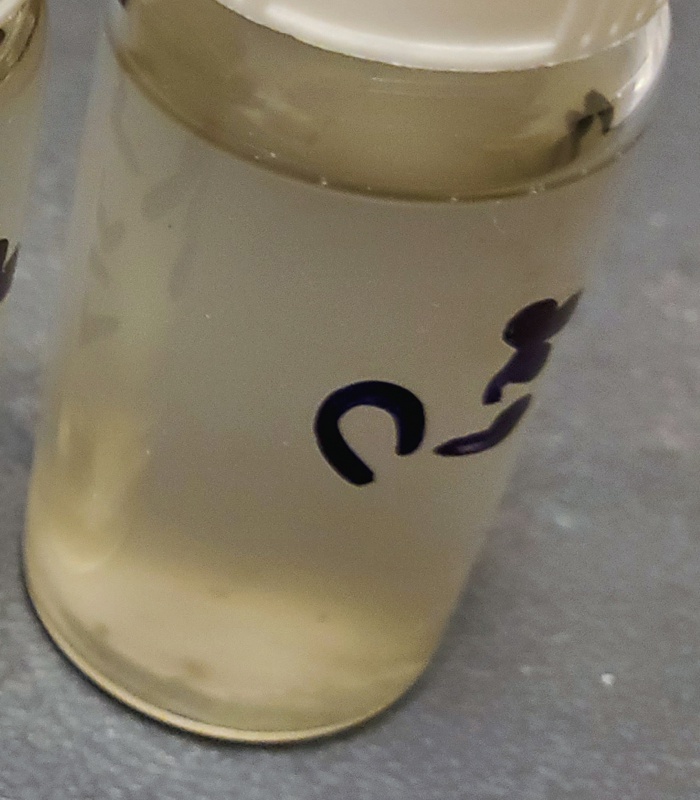
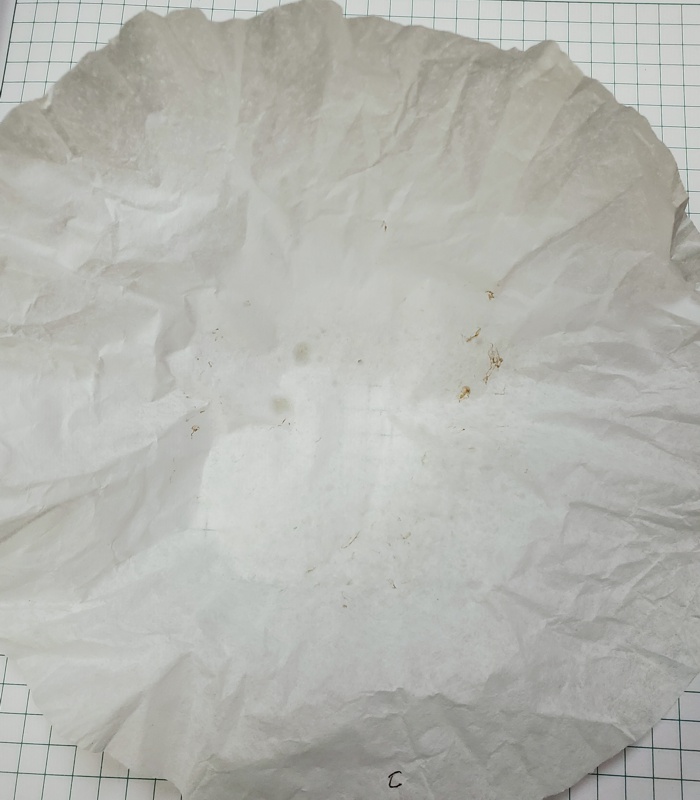
From left to right: NuPlon piece original in water, after 2 months, remaining solids on piece of filter paper after passing NuPlon degraded residue through.
Customizability
Incorporation of various additives can be used to modify the NuPlon material to provide a wide array of properties. Contact John Garner (jg@akinainc.com) to discuss customization opportunities to meet your needs.
Licensing Considerations
The NuPlon platform technology is PATENT PENDING with a priority date of filing established from provisional filing on June 25, 2020. The user’s guide presented here contains information from laboratory testing at Akina, Inc. In no way does it represent all the potential uses and considerations for the NuPlon material. Contact John Garner (jg@akinainc.com) for joint development and licensing opportunities.
NuPlon™ Applications
Electrical
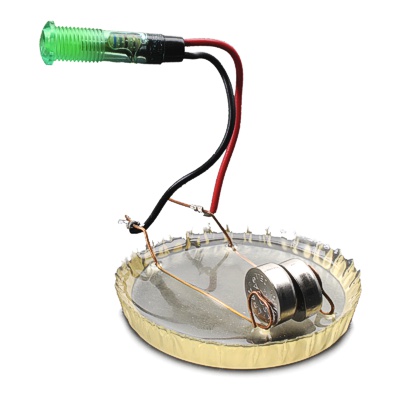
Due to it’s heat resistance and electro-insulative properties, NuPlon has the potential to find use in temporary electronics as a support/insulator board. Electrical Circuitry from NuPlon
Dyes/Colorants

Dyeing plastic to form a variety of colors is preferred for an array of applications ranging from toys to house-hold items. Using Dye/Colorants with NuPlon